Tsukiji Type: Preserving the culture of type for the future, focusing on the beauty of uneven surfaces
![凹凸の美にこだわり続け活字文化を未来に残す[築地活字]](https://magcul.net/wp-content/uploads/2018/03/d2f334f762e29d7e47eacfec80cff685.jpg)
Manufacturing
Creating things
Craftsman's Landscape
This issue's site
[Occupation] Type casting craftsman
[Craftsman name] Tsukiji typesetting Omatsu Hatsuyuki
[Location] Minami Ward, Yokohama
Carefully, slowly, and with thought.
A section introducing manufacturing sites that make use of handcrafted techniques.
This time, we will look at letterpress printing, which once supported Japan's printing culture.
Introduces the world of digitalization.
He went on to work at Tsukiji Typeface, which has gained support from many customers.
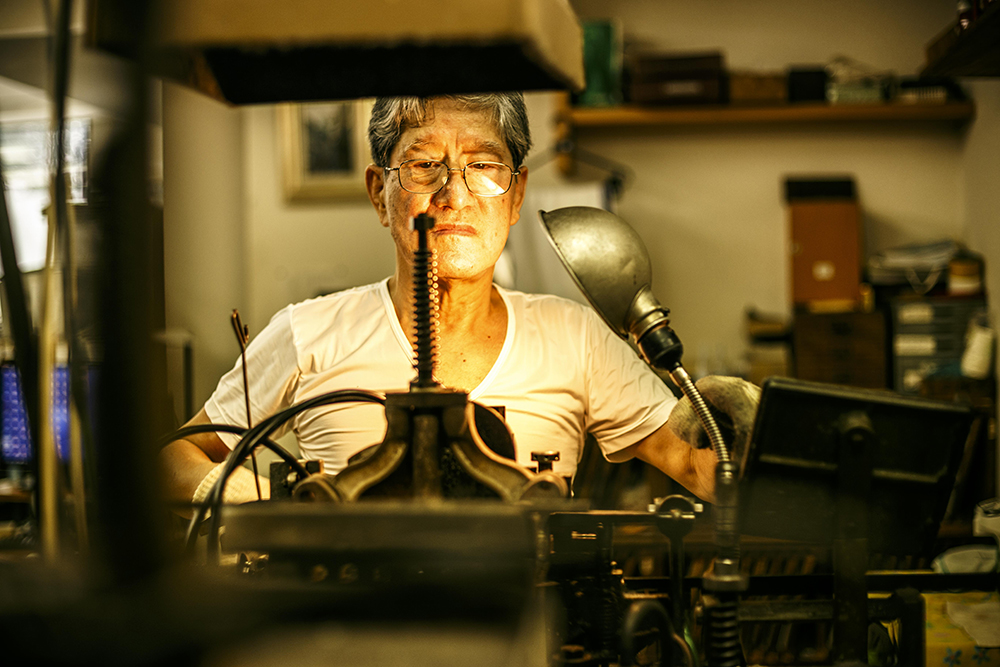
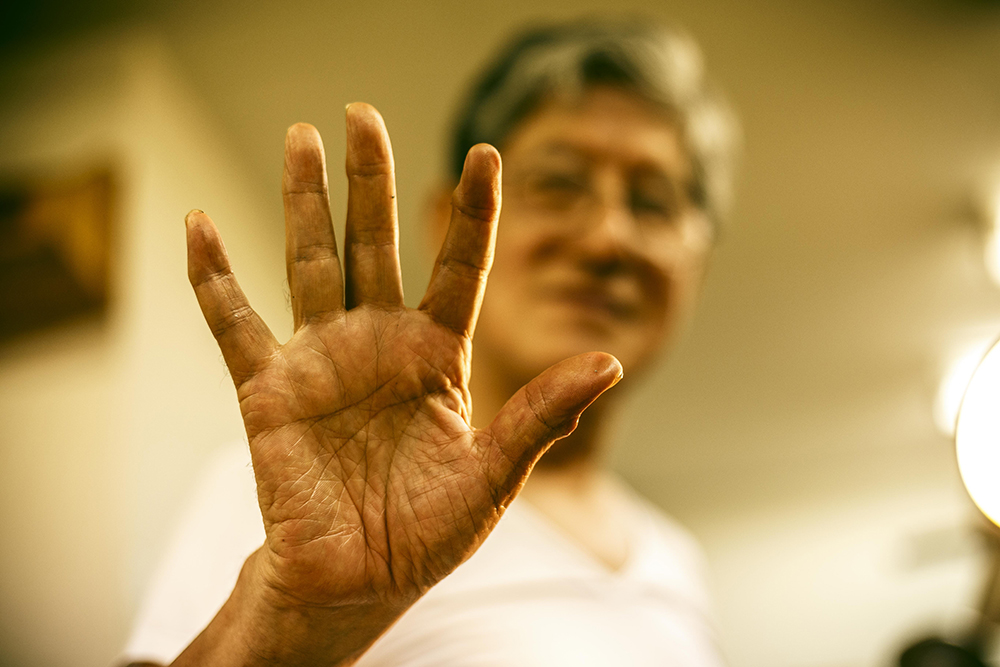
A worn wooden shelf called the "Type Room." More than 250,000 metal characters, including kanji, hiragana, and the alphabet, are lined up there. This is Tsukiji Type, which was founded in 1919 (Taisho 18). At the back of the store, a loud mechanical sound is coming from a type casting machine. The raw metal (ingot), melted in a kettle at 350-400 degrees, flows into a concave mother mold that has been installed in the casting machine beforehand, and emerges as a convex type while being cooled with tap water. Omatsu-san, who has been working as a casting craftsman here since he was 19 years old, is now 73 years old. He occasionally pulls down his glasses and peers through a magnifying glass to inspect the freshly made type. This careful and high-quality work, which has been going on for more than 50 years, still conveys the charm of type to us today.
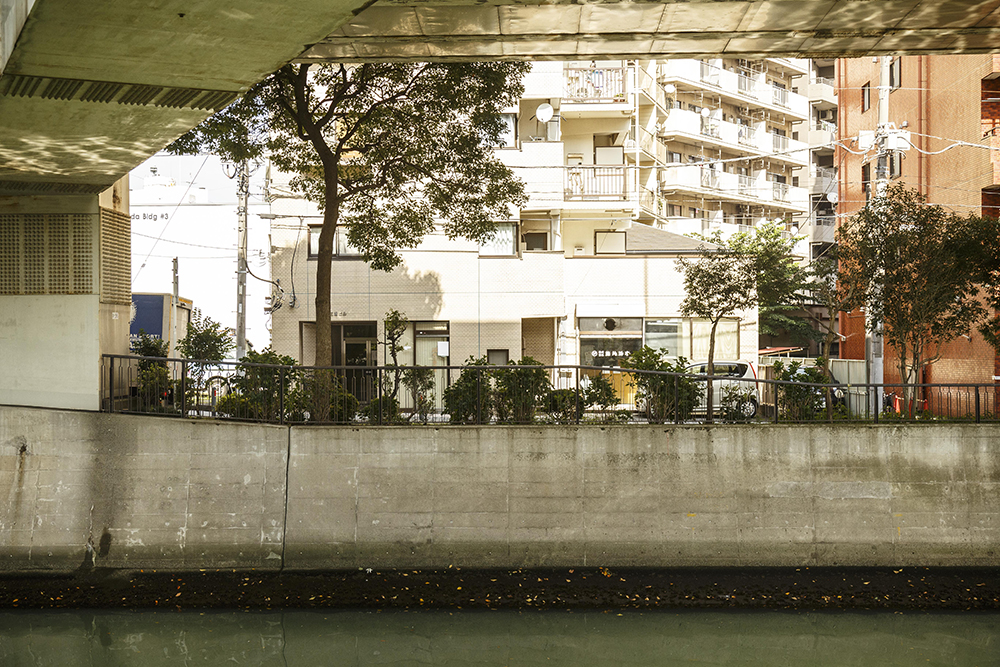
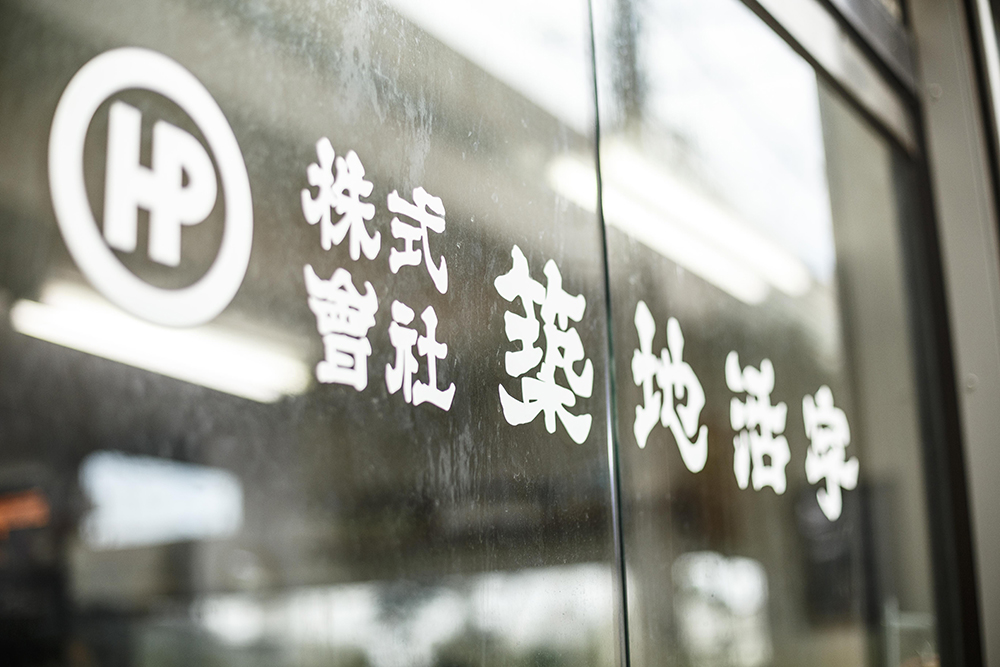
Just a short walk from Yoshinocho Station on the Yokohama Municipal Subway Blue Line. Tsukiji Type is located along the Nakamura River, which branches off from the Ooka River. When you open the door, you'll hear the loud clanging of machines and the distinctive smell of burnt oil. The source of that sound and smell is the type casting machines lined up in a row at the back of the room, where craftsman Omatsu stays by his side, watching over the machines' operation without ever leaving his side.
This time, we had the opportunity to talk with Kiichi Hiraku, the fifth generation owner of Tsukiji Type who has taken over type casting and letterpress printing.
"There's something my father, the previous president, used to say that I'll never forget: 'The letters in old newspapers are less tiring for the eyes than the letters in modern newspapers. This is because the subtle differences in color intensity on the printed surface, caused by the unevenness of the characters set using letterpress, give your eyes a rest.' I now strongly believe those words. So, in today's society where digital printing is on the rise, I feel a mission to present the artisanal techniques of creating letterpress type with "weight" to the world as the unmistakable genuine product," says Hiraku.
With Hiraku as our guide, we will be shown the various tools and techniques related to letterpress printing that have survived through the ages and are still alive today.
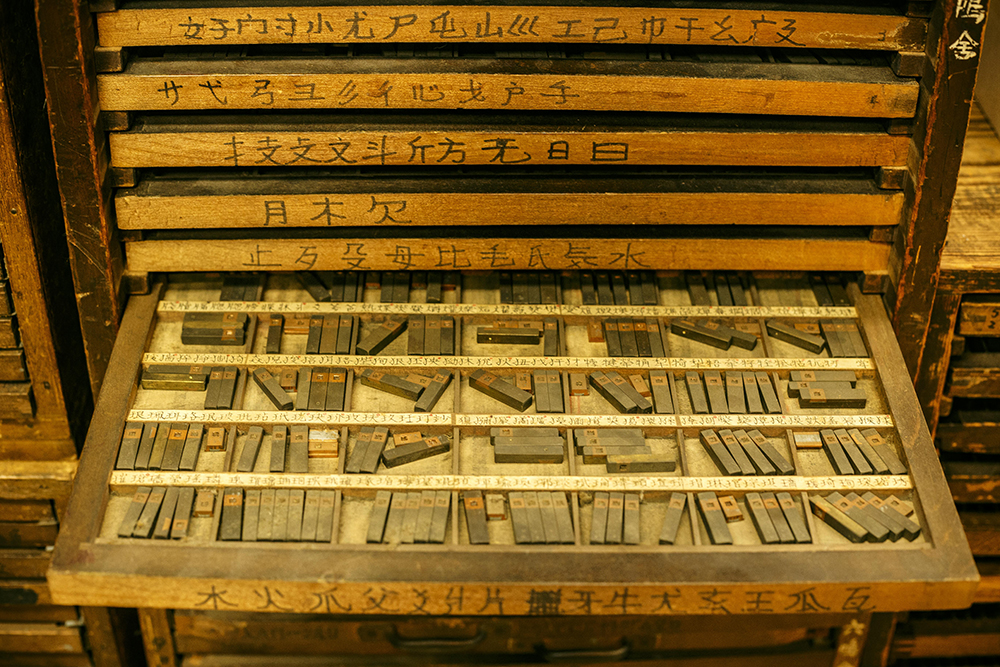
This is the so-called "matrix drawer," which houses the matrices that are the casting molds essential for making type. Opening the drawer reveals rows of brass matrices. Tsukiji Type apparently stores matrices for more than 250,000 different characters, but since there are no longer any craftsmen who make these matrices, the items stored here are extremely valuable "treasures."
This "Master Safe" also houses valuable brass master molds.
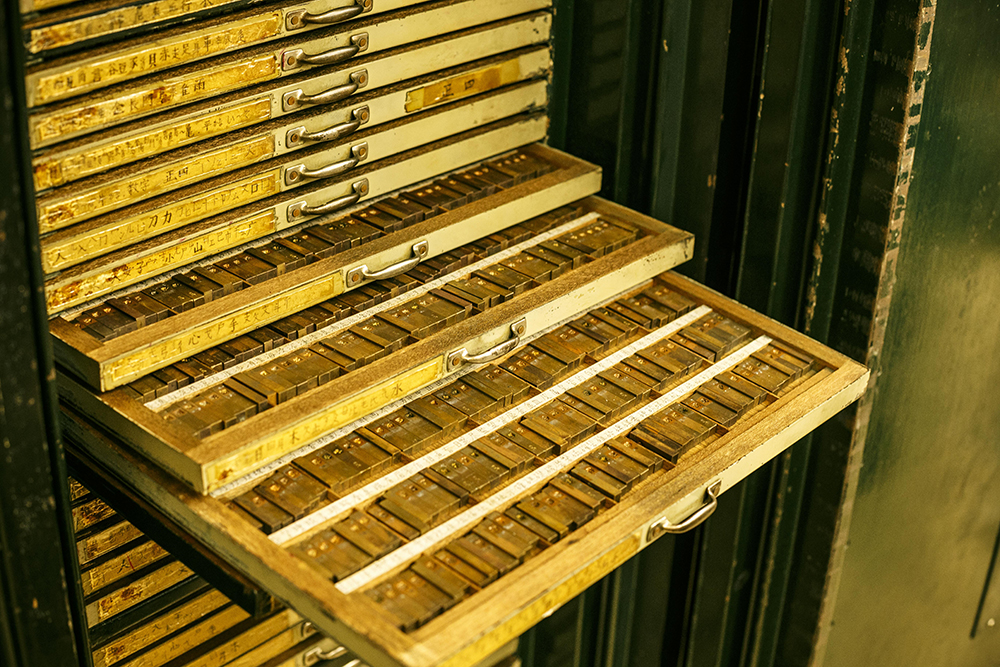
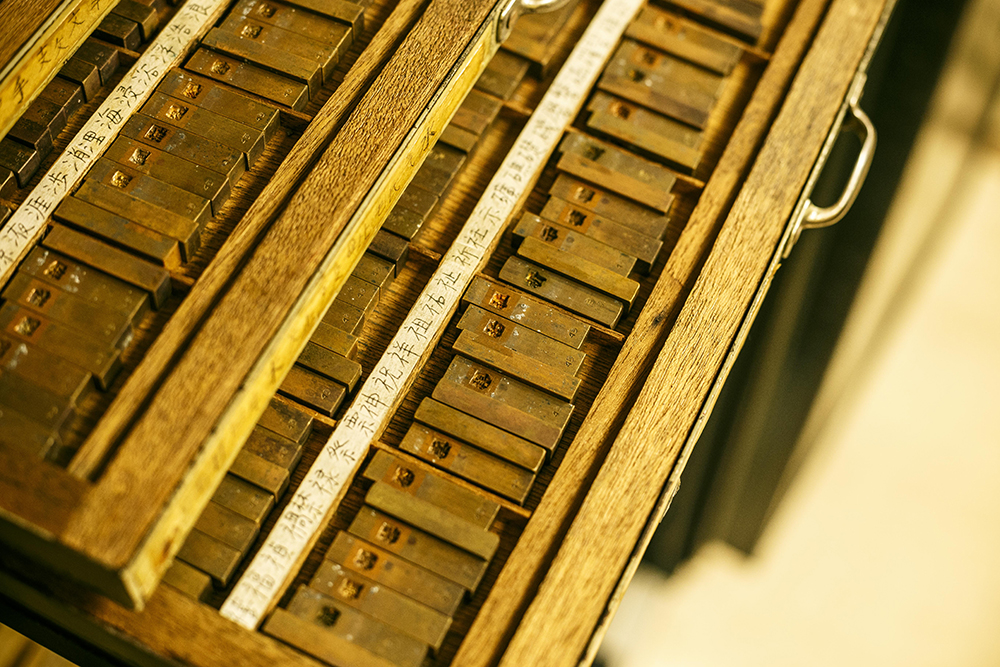
When the molten metal (ingot) is poured into this concave part, it becomes the convex type.
The next place we were shown was the so-called "type room," which was filled with type made by foundry craftsman Omatsu.
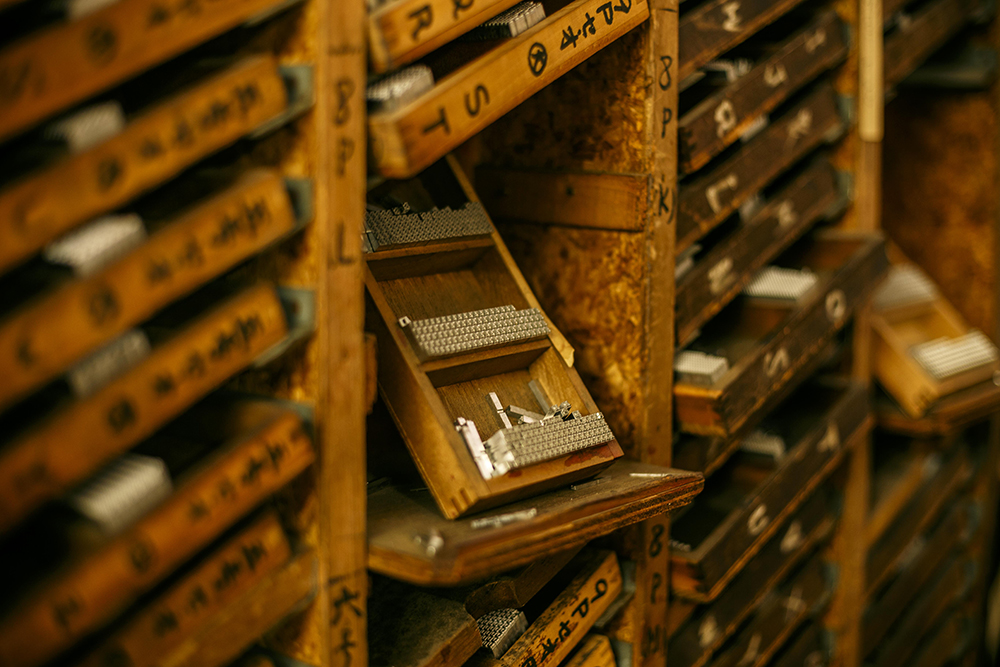
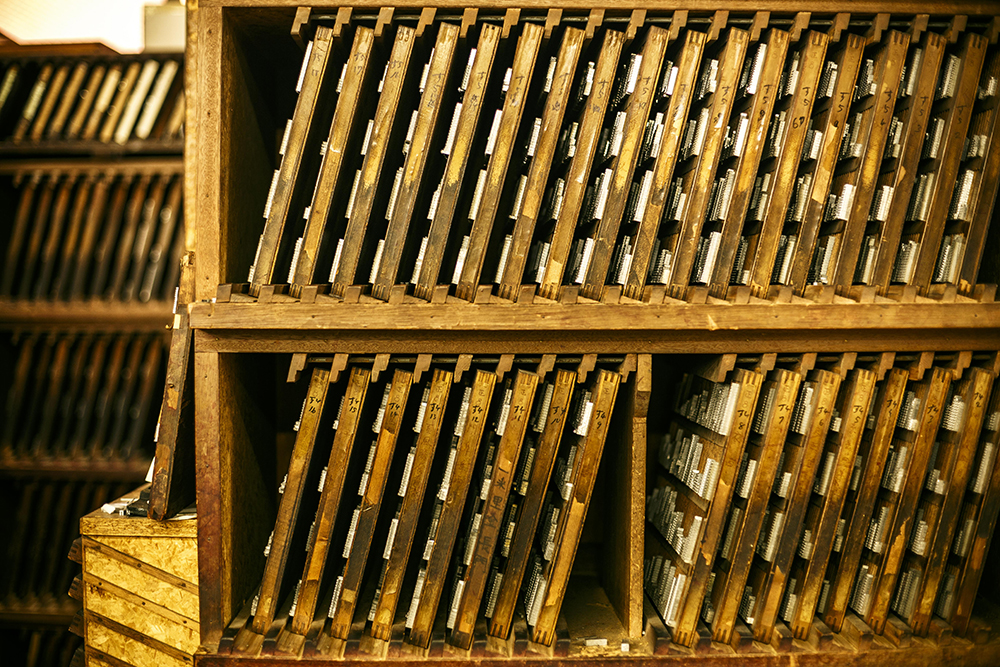
Why are the shelves stored at an angle? When I asked Hirako, he said, "The shelves with the type are stored at an angle to protect against earthquakes. Because they are designed to be very balanced, the type is less likely to fly out in the event of an earthquake, and this style has been passed down for generations." Also, the way type is arranged varies from printing company to printing company, and here at Tsukiji Type, the characters are arranged in the order they would appear in an encyclopedia.
This is a shelf for 4-point type, the smallest type available at Tsukiji Type. The job of setting type like this has disappeared.
Next, we had the opportunity to see the workplace of Mr. Omatsu, the craftsman who operates the type casting machine.
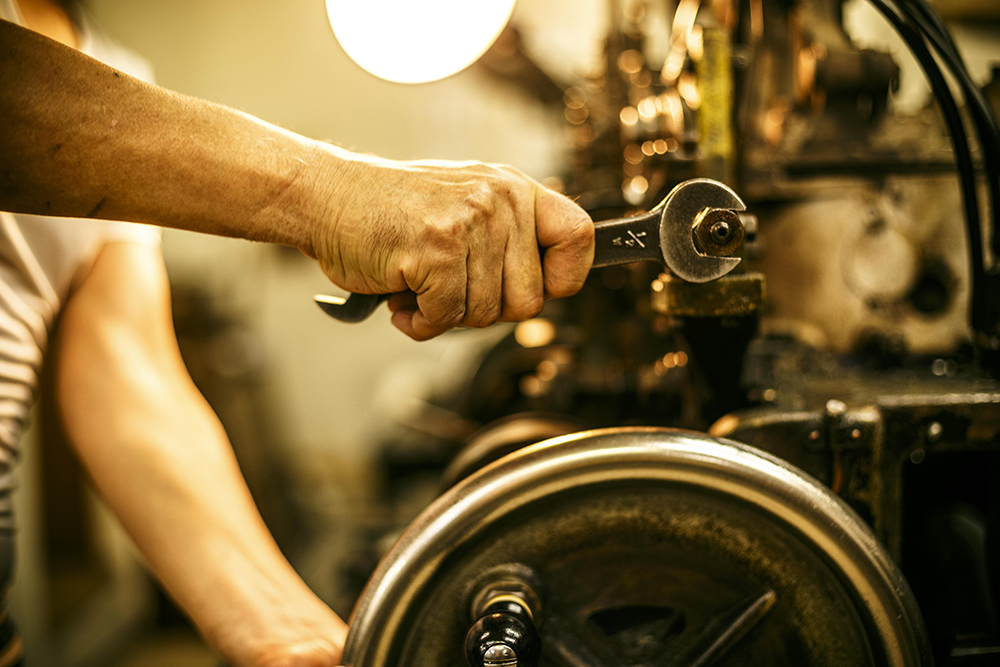
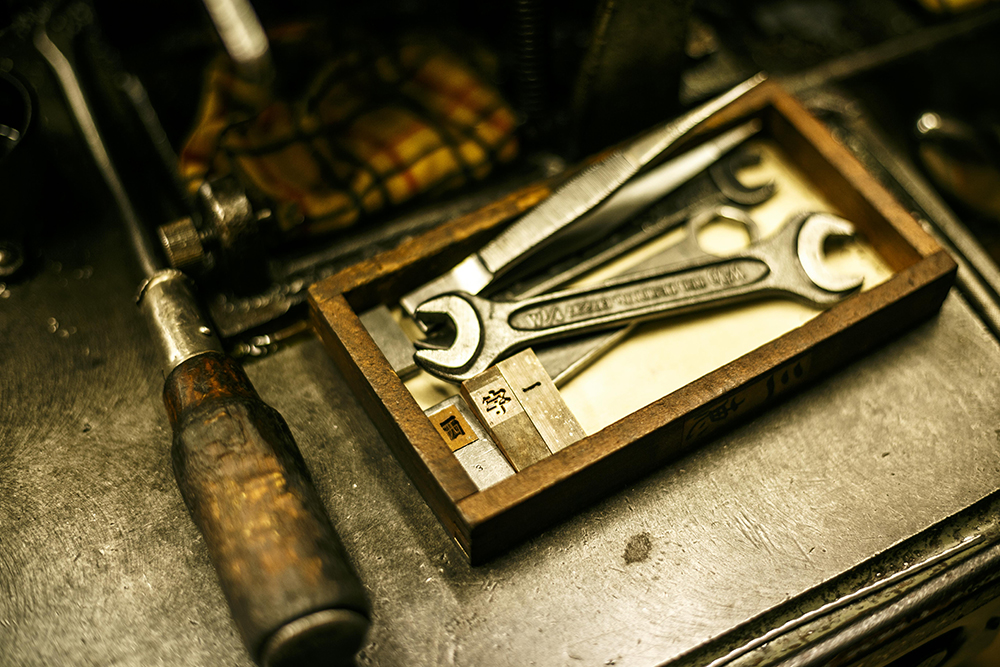
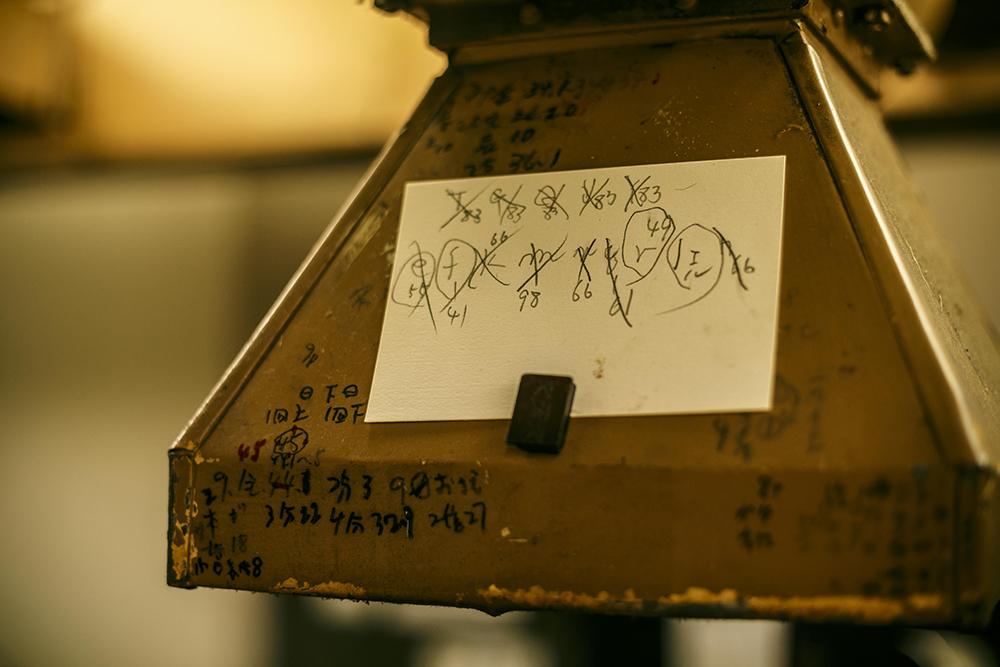
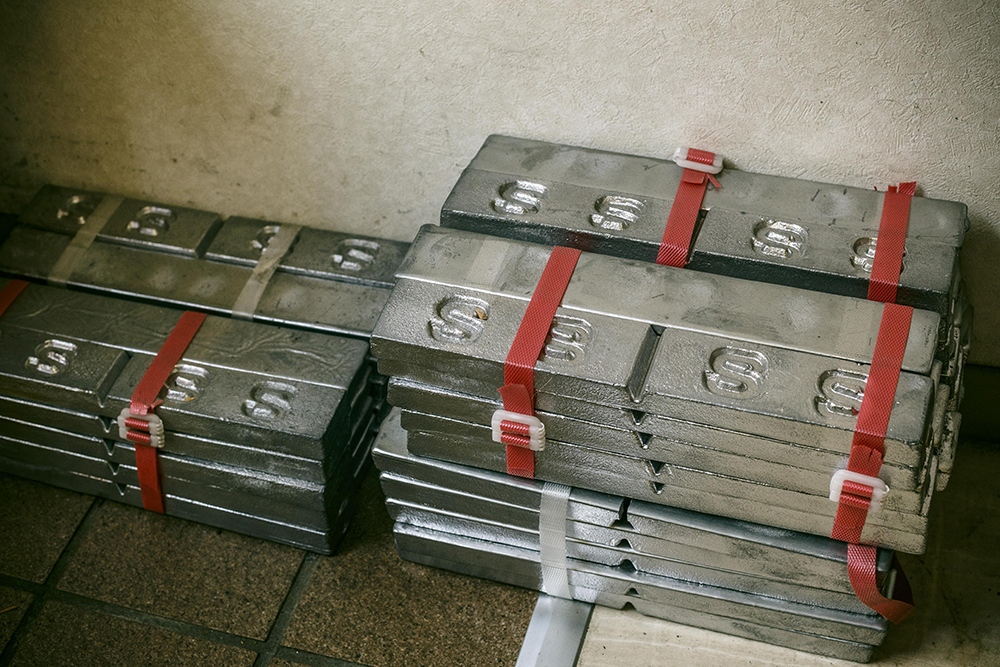
The raw metal (ingot) used to make type is 83% lead, with the remaining 15% antimony and 2% tin.
In a type casting machine, the kettle is heated to 350 to 400 degrees, melting the aforementioned bullion (ingot) into liquid form.
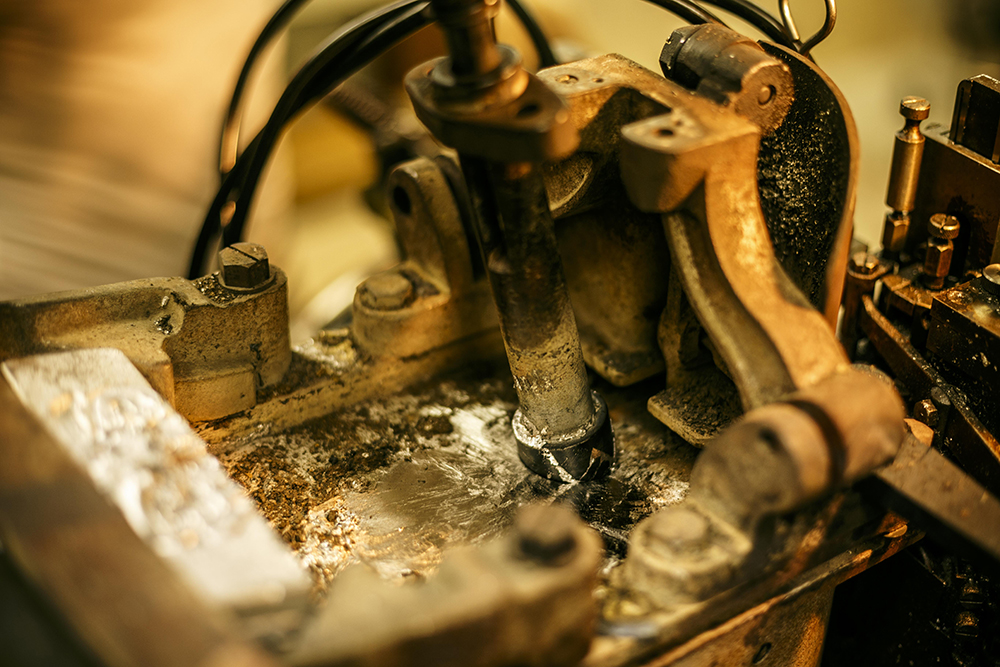
The liquid bullion has accumulated in the center.
Standing beside the casting machine, from which sweltering heat rises, Omatsu continues working for long periods of time, keeping an eye on the condition of the furnace.
A rod is placed in a pot containing molten metal and the material's specific gravity and other "feel" are checked.
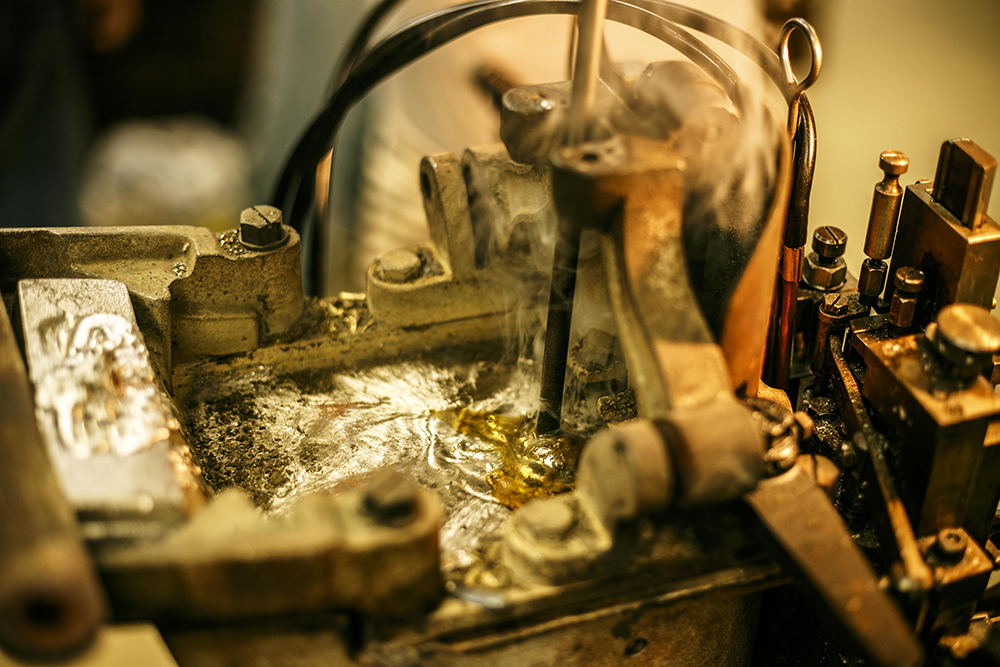
The molten metal in the kettle is then poured into the concave mother mold.
The metal that flows into the concave matrix is cooled with tap water (pictured above) and becomes convex type.
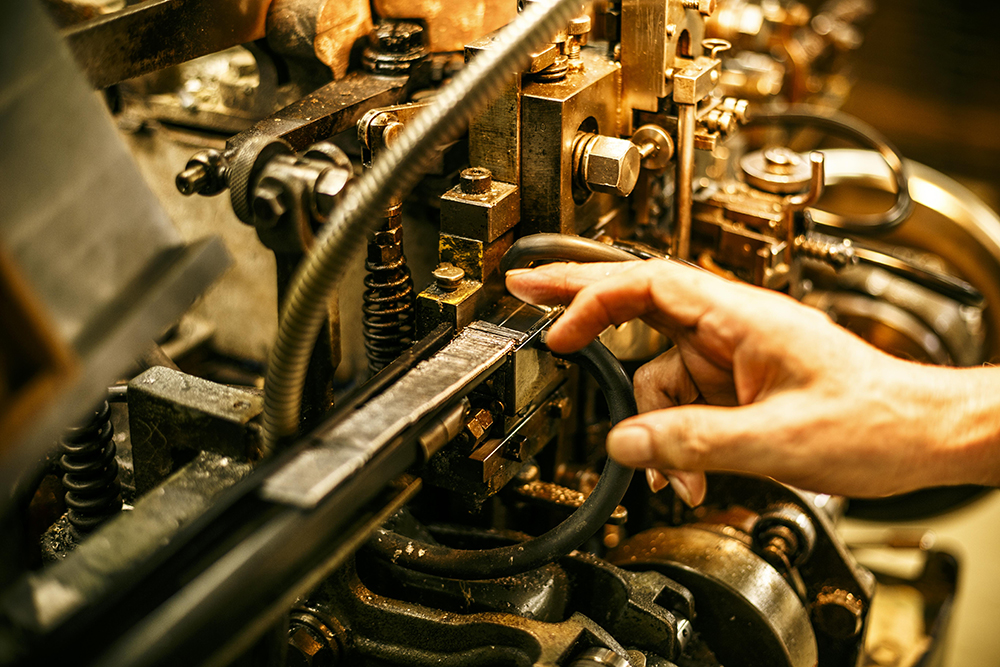
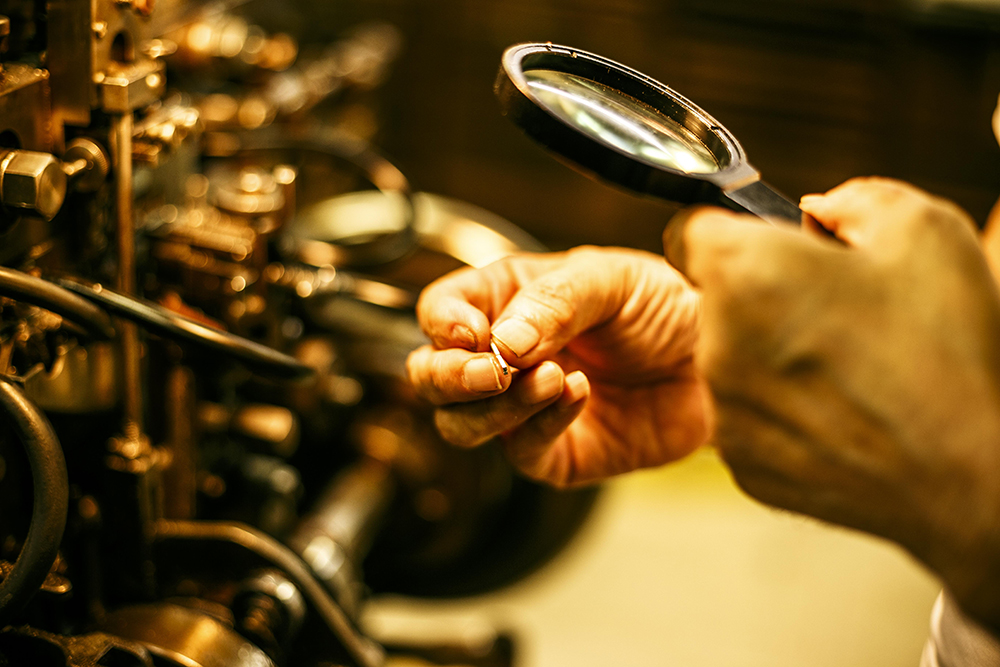
The meticulous work of checking the completed tiny type with a magnifying glass continues. These tiny type are useless if they fall to the floor, because even the slightest scratch can ruin the beauty of the type.
Because there is a risk of a steam explosion if the machine comes into contact with water, Fire Prevention Law requires that an exhaust duct be installed above the casting machine.
From here, Hiraku-san will teach us the basic steps of letterpress printing. First, type is selected in the "type room" to match the prepared manuscript, and then placed in the "type selection box." After that, the type is placed in a metal frame called a "chase" while adjusting the spacing of the characters to create the plate, but this is quite difficult. It requires not only manual work but also the craftsmanship of "eye for quality," such as exquisite use of space between characters and lines.
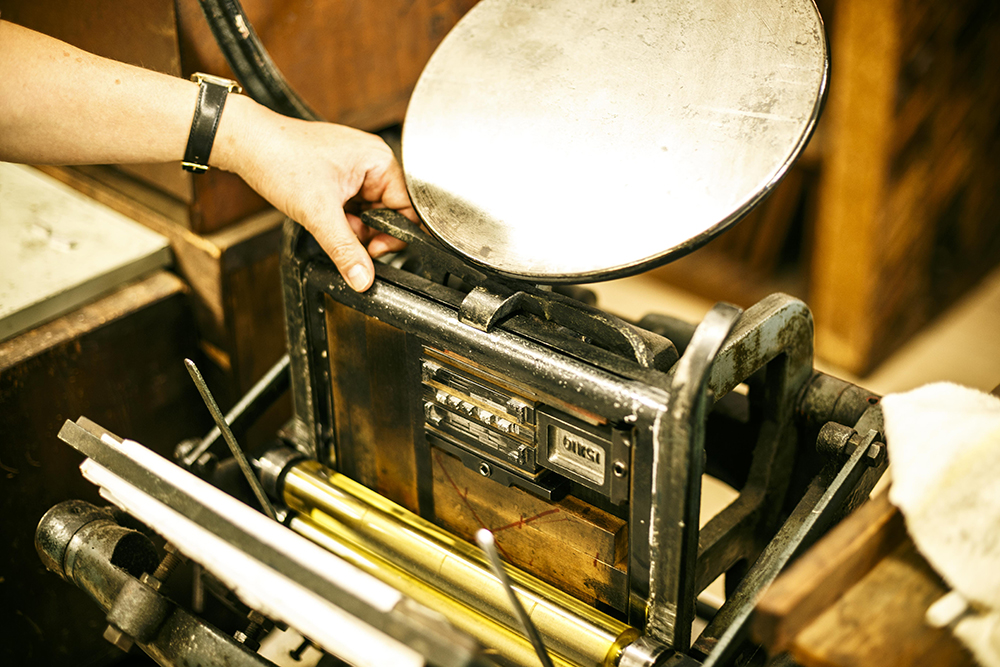
Finally, the chase is attached to a roller-equipped printing press, the ink and paper are added, and printing is completed.
Tsukiji Type also sells type holders, which have been developed to make beautiful letterpress type more accessible and to be used for a variety of purposes. "I want people to experience the fun of setting and printing type themselves with this small tool," says Hiraku.
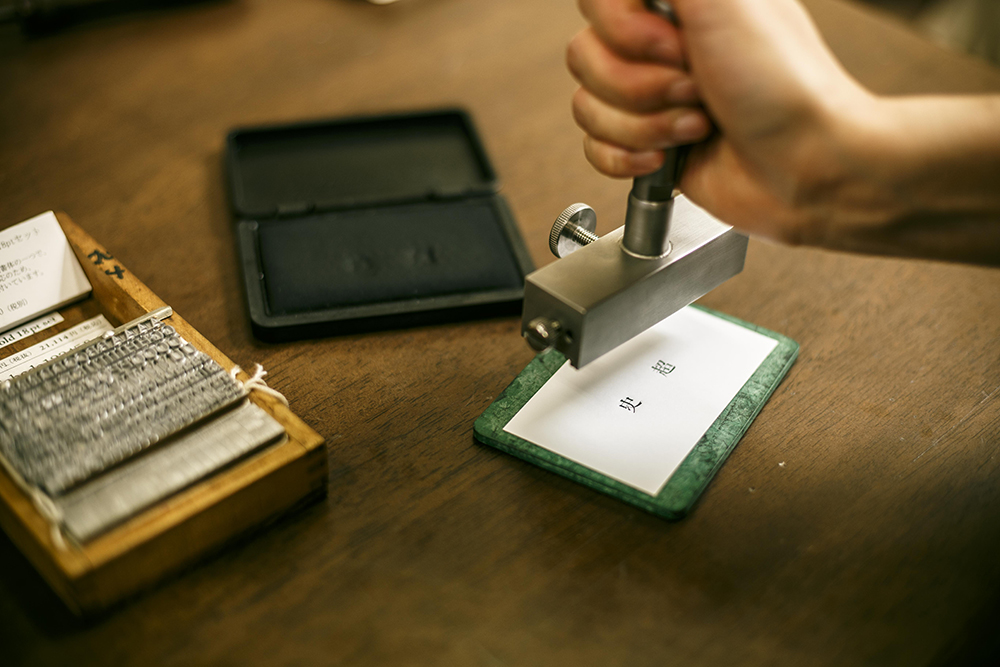
As an aside, I thought the appeal of letterpress printing was the deep unevenness (even the back side is uneven) that appears as if it is engraved into the paper, but he said, "It has been said since ancient times that artisans who are too forceful in letterpress printing are no good. The key to skill is to express beautiful unevenness on the front side while preventing it from showing through to the back side and changing the appearance of the paper on the back side." I was able to hear many profound stories.
When I receive a letterpress business card for work, I can't help but pick it up and stare at it. Today, I realized the reason why. It's just a business card, but it's still a small square piece of paper that fits in the palm of your hand, and it is engraved with the skills and thoughts of artisans that have been passed down for generations. Why not try letterpress printing not only for business cards, but also for New Year's cards from now on? A New Year's card that will make people who pick it up fall in love with the beauty of the letters and want to touch them with their fingers.